Get the Best Products from Wedge Wire Screen Manufacturers
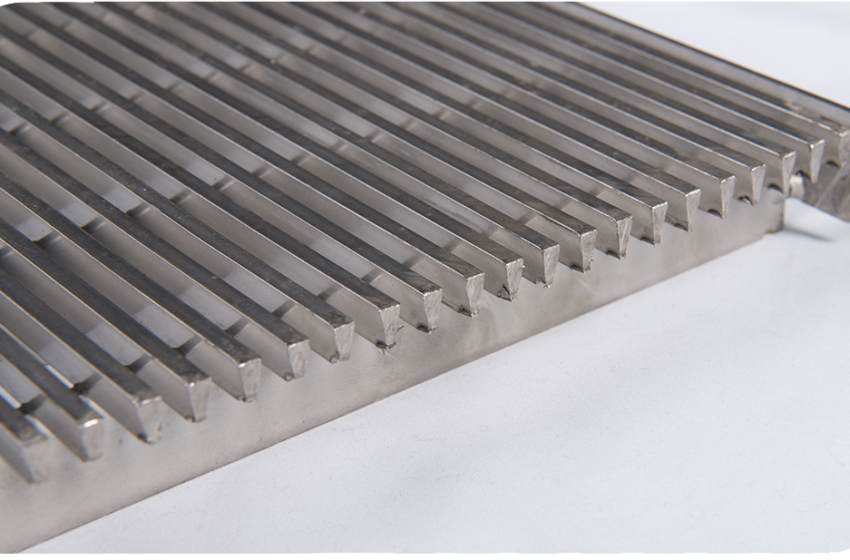
The number and complexity of industrial processes and applications are staggering. We will go through wedge wire screen goods, their benefits, and the applications they can use when bought from the best wedge wire screen manufacturer.
What is an Industrial Wedge Wire Screen?
To generate a structurally sound plug-resistant surface, all wires and ribs are resistance welded at each contact poi. Wedge wire screens provide a wide range of combinations, allowing for perfect matching to technical criteria. They can be found in practically any alloy and are utilized in various industries, including water treatment, food and beverage, oil and gas, pulp and paper, mineral and aggregate processing, and petrochemicals.
Wedge Wire Screen Manufacturers make them to Separate Liquids from Solids
Wedge Wire cylinders are used for rotating screens, collectors such as screen laterals and nozzles, resin traps, in-line Wedge Wire strainers, water intake screens, well screens, and various other liquid/solids separation applications.
Wedge Wire screen cylinders can be built with slot holes and wires running radially on the screen cylinder’s exterior surface or axially on the cylinder’s inside cover.
Screen cylinders are available in various sizes, ranging from 1/2″ to 35″ at wedge wire screen manufacturers. The diameter of screen cylinders can be increased. Each wedge wire and support rod junction is welded for further strength and longevity.
Different Types available at Wedge Wire Screen Manufacturers
Catalyst Bed Supports — These screens are built to last, have a precise open area, and are nearly clog-free. Their support grids ensure that media is retained better in all sorts of vessels. Grids for larger vessel diameters are made in parts to allow manway installation. They can be equipped with an inlet basket, distributor lateral, support grid, and outlet basket, as well as backwashing systems.
Hub and Header Laterals – These screens are suitable for disc head vessels that require the system to collect to the vessel’s bottom ultimately. The lateral design of the header can also be employed in distributor or collector applications with a flat bottom vessel. Side, center, top, and bottom inlet pipes can all be accommodated by screens.
Integral backwash systems regarding fast and effective cleaning are available on hub and header laterals. Systems can develop for liquid or solid retention for applications such as exchangers, clay and sand filters, carbon towers, and power plants with water systems.
Nozzles and Strainers – Retention nozzles can produce in practically any metal to meet flow requirements. They can be made for filtration or treatment systems, allowing increased media usage. Water treatment and other industrial applications use non-clogging wedge wire nozzles, such as under-drain media retention elements, flow distributors in demineralizers, pressure water softeners, and gravity sand filters. They can also be used as bottom vessel collectors on a tray plate with a large open area that is not pluggable.
Sieve Bend and Flat Screen — This solution is ideal for high-capacity filtration because the screens are sturdy, reusable, and self-cleaning. Water can fall through Sieve Bend screens for collection, but solids can slide overdue to the angle and flow. These screens are helpful for sewage separation, dewatering, and wastewater treatment.
Resin Trap Screens — The screens are usually installed in housing in line with the flow to prevent expensive media from going downstream. Traps can trap particles of any size while still allowing the process to flow smoothly.
Wedge Wire Screen Manufacturers have all these types of screens and are also perfectly made for all applications.