How to Maximize Drilling Efficiency With Fluid System Maintenance
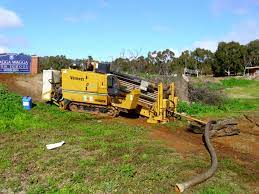
Maintenance of equipment is never a trivial task, but it carries a little more weight when it comes to directional drilling.
A field-based equipment failure caused by poor maintenance entails more than just rig downtime. It could also mean abandoning a hole midbore and starting the process from scratch again.
Whenever directional drilling is concerned, the drill gets the most of the attention. But fluid management systems can’t be overlooked if you want to reduce downtime on the job site. Fluid mixers and reclaimers are the two main pieces of equipment in this category.
If you provide directional horizontal drilling services, keep these maintenance guidelines in mind.
Start With The Fundamentals.
A gas or diesel engine, like other heavy equipment, is a vital component of fluid handling systems. Hence frequent engine maintenance is critical. Engine oil and oil filter should be checked daily, as well as any manufacturer-recommended maintenance intervals.
Pumps are used in all of this equipment, mainly centrifugal pumps on mixers, which have their own set of issues.
Impellers move the fluid in centrifugal pumps, and when those impellers wear out, you may lose head pressure in your hydrocyclones. When head pressure is lost, the hydrocyclones lose their cleaning capacity. Thus, it’s crucial to keep an eye on that head pressure and make sure the centrifugal pumps are in good working condition.
Cleanliness Should Be Observed.
Drilling can be a messy project, but cleaning up after each job is vital for your equipment as well as the site.
Tanks and hoppers in mixers and reclaimers cycle through a range of materials. In between jobs, keep them clean to avoid cross-contamination in your fluid, as well as rust and other impacts that might shorten the life of your equipment. There may be a propensity for solids to settle out of the tanks after each cleaning. That said, getting those solids out of those tanks is critical.
Also, if water stagnates in the tanks, algae may develop. Moisture buildup in the dry hopper of mixers can cause major clogging, resulting in job downtime. To prevent such issues from arising, it’s recommended to implement cleaning routines right after the equipment is used.
Maintaining The Drill Should Be Done On A Regular Basis.
Fluid handling systems improve horizontal drilling efficiency, but if not used properly, they can cause difficulties with the drills. Mixing systems enable the right combination of drilling fluid, but the machine’s variability necessitates caution.
Perform tests for density, viscosity, pH, and sand content. In terms of the drill rig, it’s best to do a lot of testing for performance and long-term durability.
Also, making sure you have the appropriate mix is crucial not just for job productivity but also for ensuring that your drill lasts as long as possible.
Not keeping a tight check on the reclaiming end of the drilling process can have negative consequences for the drilling system as well. The shaker deck, where a number of screens prevent spoils and other debris from infiltrating the drill, is the most critical section of a reclaimer.
On reclaimers, it’s all about screen maintenance:
- keeping your screens clean;
- inspecting their condition;
- and replacing any screens that have holes in them since your contaminates are being returned to your tanks.
Screens should be inspected on a regular basis too. It depends on the material, but it’s not unusual to go through numerous screens in a single job. They wear out due to vibration and abrasive materials like sand that slide across them.
Takeaway
Directional drilling is a high-stakes, high-stress job, and anything that can be done to make it go as smoothly as possible is time well spent. That’s why fluid handling systems and ensuring that they’re running at maximum efficiency are crucial considerations for every contractor.