The How-Tos of Managing Drilling Fluids on HDD Projects
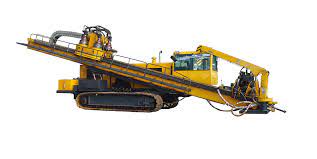
Preparing the drilling fluid can be a time-consuming process, so it is best to spend some time preparing by learning about your equipment and how different types of fluids work with it. You should also learn about the industry standards for drilling fluids and how to test them.
Take some notes before beginning work with each new type of fluid to be able to reference them when needed, especially if you are working on the first job of the season.
A drill-site visit is also a good idea in order to familiarize yourself with the specific project and get an overall feel for how you will manage your fluids. Always make sure that you have everything ready before beginning work, even if it is just a test run.
Using the Right Fluid for the Right Application
Depending on your drilling application, you will need to prepare different types of fluids that can do specific jobs. For example, if you are only drilling without turning, a non-gel type fluid may be appropriate. However, if you are running tools through your borehole, such as a drill or gravel pack gun, you may want to choose a gel type fluid.
If you are drilling in an area that is susceptible to washouts (onshore areas with sandy soils), mud rheology modifiers will help prevent improper set-up and other problems. Antifoam additives can also be added.
If you are changing the fluid in the hole, try to use a lubricating fluid that has particles that are similar to those of your existing drilling fluid.
This can help keep down grit and reduce wear on both equipment and personnel. It is important that you also select the correct mud weight for your application, as this determines how much cuttings will be suspended in the fluid.
Testing Your Drilling Fluids
Even though fluids may have a high gel time, they may not perform well at your site if they fail to set up properly. Fluid that sets up slowly can cause problems such as pipe sticking and can make cleanup on the surface more difficult.
If you are concerned about how well your drilling fluid will set up at the site, you can test it using a simple test.
Testing is very easy to do and only requires an old drill string, a long drill pipe joint or other section of open pipe on which the drilling fluids will not stick and some water.
- Use 5 gallons of fresh water for every 100 gallons of drilling fluid and place it on the pipe.
- Let the water sit for 5 minutes to ensure that any air is out of the liquid.
- After 5 minutes, record how much water has drained from the pipe. If 6 gallons or more have drained in a 5-minute period, you should be okay.
However, if less than 4 gallons have drained, you should consider using another fluid for the job.
Drilling Fluids and Gels
Gel fluids are used in most directional drilling applications, as they can help prevent washouts and keep tools moving smoothly through the hole. They also harden quickly, which makes it easier to clean up on site. And if you want to use a gel in your hdd crossing drilling project, you can speed up cleanup by using tools with longer hoses and pads.
Normal gels usually have a viscosity of 2500-4500 cP (centipoise) at the surface, but if you are working in an area where there are more cuttings or drill solids present, try increasing the rheology modifiers to help thicken the fluid.
Always use a gelled drilling fluid for directional drilling jobs, as non-gelled fluids tend to break down too quickly. However, make sure that you don’t over-thicken the fluid by using too many additives or too much bentonite. Also, be careful not to add too many solids, as this can cause the fluid to set up too quickly.
Checking and Changing Fluid Levels with a Drilling Fluid Management System
A drilling fluid management system is one of the easiest ways to properly check levels in your hole at all times. This type of tool helps you easily determine how much water, clay and drill solids you have in your hole, as well as how much you are pumping.
A drilling fluid management system consists of a tool string and pressure-sensing devices that you attach to the drill string so that they hang down into the borehole. The pressure sensors send information to a computer, which tracks your mud levels in real time. This software displays how much drilling fluid you have, what the viscosity is and how many drill solids are in your hole.
These tools can help prevent problems such as over-drilling or washouts because they constantly monitor your mud levels.
When you use a drilling fluid management system to check your mud levels, remember that some of the measurements may be inaccurate due to fluctuations in temperature, pressure and other factors.
Using Desander Drilling Fluids for Shallow HDD Projects
A desander is a drilling fluid tool that removes saltwater from mud used in directional drilling projects, making it safer to use at shallow depths. This type of fluid can also be effective at increasing the life of your drill pipe and drill bits, which reduces downtime and other expenses.
Desanders are typically used on wells that begin at depths of 300 feet or less. They come in two different types: those with a desilter and those without a desilter. A desilter is an addition to the desander system that removes any suspended solids, returning clear mud to the hole.
A desander is typically used only in low-pressure wells, although some companies use them for their hdd crossing projects. They aren’t very effective at removing drill solids and clay from higher-pressure wells. Before you start using a desander to clean out your well, make sure that it can meet your drilling project’s requirements.
When you’re choosing a desander, keep these factors in mind:
- Does the system have any leaks? You don’t want one that will waste fluid and time.
- Can the tool withstand high-pressure wells? If not, it may not be able to complete your drilling project.
- Does the tool work quickly and effectively? Be sure to find out how long it takes to clean your well, how many parts it requires and other details about its performance.
Takeaway
The fluid used in drilling was formerly solely thought to be useful for bringing rock cuttings to the surface, but it now has a wide range of applications, especially in trenchless construction. The drilling fluid serves other, equally vital usage in addition to lifting the cuttings in order to complete the drilling operation in a safe, efficient, and economical manner. Thus, following a management system is a must for every drilling project to ensure success and avoid environmental repercussions.